Kappa X Prevents Catastrophic and Costly Failure at Power Plant
- Apr 1
- 3 min read
Updated: May 22
One of the largest power plants in the United States experienced critical issues with two out of three recirculating pumps, each essential for generating power. Despite regular monthly vibration data collection, the pumps were running louder than normal, indicating a potential problem which required urgent attention. The plant implemented a continuous monitoring strategy using Sensoteq’s revolutionary wireless sensor Kappa X to avoid costly machine failure and downtime.
Machinery and Operations
The client’s recirculating pumps are essential for generating power by providing deionised water to produce steam for the turbines. A complete pump failure would result in a catastrophic power outage. Furthermore, replacing one of the pumps was estimated to cost $120,000 and would take approximately 16 weeks, causing significant financial and operational setbacks for the power plant. The site is located in the desert and must recycle all water to ensure maximum sustainability. The ZLD area at which the pump operates is also critical to clean up the pond water to ensure the site maintains zero liquid discharge from the facility.

Implementation
To monitor for machine faults and failures, two Kappa X sensors were mounted on the motor bearings and two sensors were placed on the pump bearings. By utilising a condition monitoring strategy, the maintenance team could receive vibration data, analyse the findings and address potential issues. Kappa X sensors and the intuitive Sensoteq Analytix software would help them detect machine inefficiencies and possible failures.

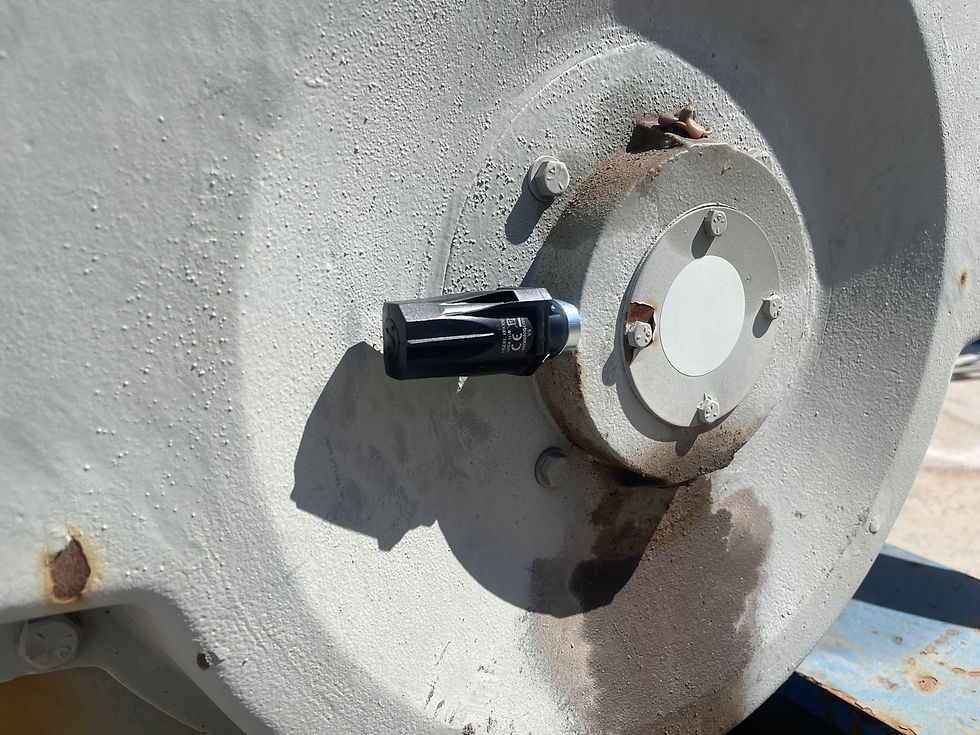
The Problem
After a period of continuous monitoring, the collected vibration data indicated a potentially costly ongoing issue with the pump. The vibration for the pump drive end bearing exceeded the warning alarm threshold almost immediately and the critical alarm was triggered shortly after on multiple occasions. The vibration for the pump non-drive end bearing followed a similar trend, surpassing the warning alarm line and exceeding the critical threshold to a level over 0.5 in/sec RMS. The vibration data graphs below demonstrate how the pump was rapidly approaching catastrophic failure.

The Solution
Due to the concerning spike in vibration for each bearing, plant personnel swiftly decided to shut down the motor pump assembly for an essential service, prompted by the alarming trend observed in the data. To avoid a complete failure, a certified rotating specialist was brought in to completely overhaul the entire pump assembly. This proactive and decisive action ensured that potential issues were thoroughly addressed, safeguarding the plant’s operations and ensuring machine efficiency.

During the overhaul, a careful examination of the pump power frame revealed significant damage. The pump power frame and mechanical seal were replaced to rectify the issue. The Kappa X data played a critical role as the contractor could reuse the existing CD4 wet end of the pump which has a lead time of over 6 months. Had the Power frame completely failed, the pump impeller would have made contact with the volute, rendering it unrepairable and bringing the unit down for an undetermined amount of time until a new wet end could be installed.
The data from Kappa X also revealed that the discharge strainer baskets were completely clogged, causing the pump to run at an extreme deadhead. This condition destroyed the thrust bearings in the pump power frame and resulted in extremely elevated vibration levels across all three planes of the triaxial sensor.

The Result
A meticulous precision alignment was conducted to ensure proper machine functionality. Following the overhaul and alignment procedures, the pump impeller was re-installed. Upon startup, the site observed a significant reduction in vibration amplitude and improved pump performance.


The power plant was satisfied with the results achieved through continuous monitoring and timely intervention, avoiding the substantial expense required to purchase a new $120,000 pump. Impressed by the outcome, the plant expanded the monitoring system by adding additional Kappa X sensors to their other recirculation and boiler feed water pumps.
Implementing continuous monitoring using the Kappa X wireless vibration sensor enabled the power plant to detect an impending failure in one of the critical recirculation pumps. By promptly overhauling the machine and completing the alignment procedure, the client prevented a catastrophic failure, saved significant costs, and minimised machine downtime.
Don’t let machine failures disrupt your operations or increase maintenance costs. Invest in our revolutionary Kappa X sensors and employ a proactive approach to condition monitoring. For more information on how our system can minimise your machine downtime and significantly reduce your costs, contact us or book a demo.
Case study supplied by our partner https://ludeca.com/